Discover how Kimi’s helmet was born
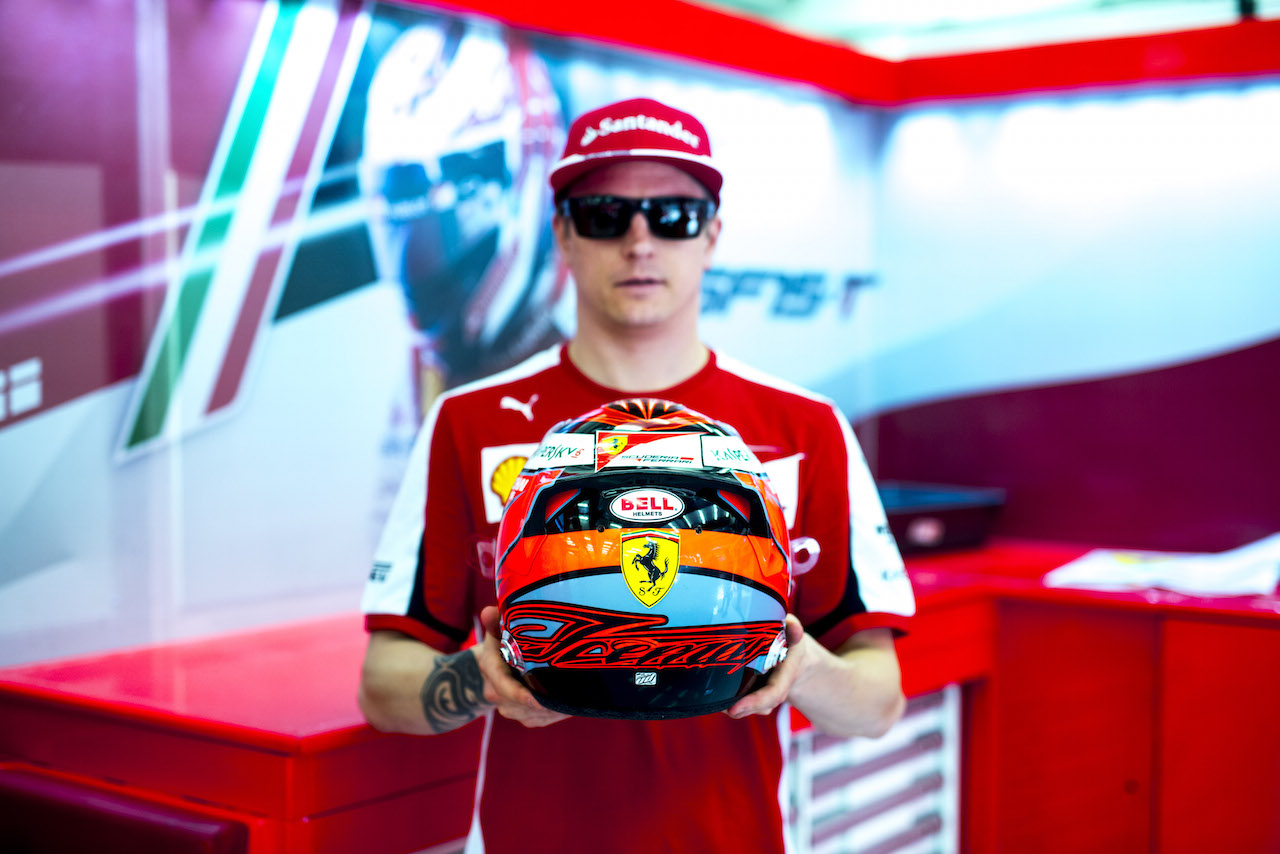
In the factory that Bell Helmets Racing has built a few meters from the entrance of the Al Sakhir circuit, in Bahrain, a new helmet was made for Kimi Raikkonen. This is step by step how it was done:
The parts of pre-impregnated carbon fiber are cut into specific shapes before being placed in a shell mould.
Up to 40 pieces of carbon fibre are positioned very precisely in a female mould. This is called the "lamination" of the shell.
When lamination is completed, the shell goes into an oven at 150 °C under vacuum for 30 minutes. This is a shell coming out of the oven.
The opening for the visor, called the eyeport, and the excess of carbon in the lower part of the shell are cut with a jig saw.
Now the shell already looks like a real helmet... The technician will now position the shell in a jig, allowing him to precisely trim the 12 ventilation holes on the helmet.
To obtain homologation, the helmet must pass a series of tests including penetration. This test consists of a spike weighing 4kg being fired into the helmet at a speed of 10 meters per second. Bell uses a special machine for this kind of test, developed and built in-house.
The shell is being prepared for painting by being carefully hand sanded...
The shell receives a thin and smooth layer of clear coat, before being personalized into Kimi's design.
The interior parts are now fitted inside the painted shell.
Finally, the transparent aerodynamic spoilers and the air intakes are glued onto the helmet, and here we are…
…ready to go!
Ferrari S.p.A.